When it comes to soldering, one often underappreciated yet critical component is soldering flux. Its role is pivotal for ensuring robust and reliable solder joints by preparing metal surfaces during soldering. But does soldering flux go bad? What happens to soldering flux as it ages? Does it lose its effectiveness? This article delves into the shelf life of soldering flux, its degradation signs, and the impact of using expired flux on soldering quality. We will also cover the proper ways to store soldering flux to maximize lifespan and performance, ensuring you don’t encounter unexpected setbacks in your soldering projects.
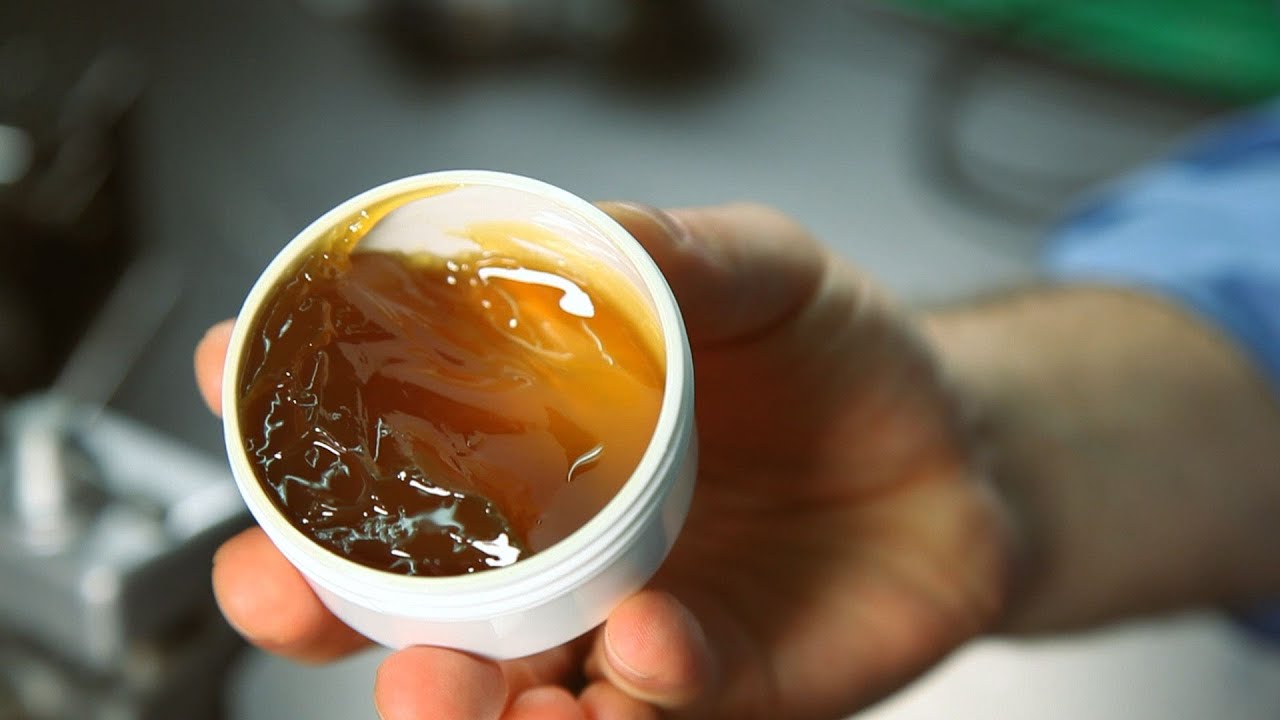
Does soldering flux go bad? How long does it last?
Soldering flux does not necessarily “go bad” in the traditional sense, but it can degrade over time, especially if not stored properly. Flux typically has an expiration date of about 2 years if purchased on its own. However, the flux cores inside solder wire are generally considered not to expire, especially if kept in a sealed bag. The unopened shelf life for brazing flux is typically 1 year, according to the American Welding Society (AWS) specification.
Flux can dry out and harden, especially if exposed to air. If the flux dries out, it can be restored by adding a few drops of alcohol if it thickens. Water may also be added incrementally to a more complex flux to convert it to a thick paste consistency.
How to tell if your soldering flux goes bad?
Here are some signs and tests to determine if your soldering flux has gone bad:
- Expiration Date: Flux typically has an expiration date of about 2 years if purchased on its own. However, the flux cores inside solder wire are generally considered not to expire, especially if kept in a sealed bag. Always respect the expiration date on any material you buy. If it is expired, it’s recommended not to use it.
- Physical Changes: Flux can dry up and become harder, especially if exposed to air. If your flux has significantly changed in consistency, it might have gone bad. If the flux has dried out, it can sometimes be restored by adding a few drops of alcohol.
- Flux Wetting Test: A flux wetting test can be helpful to determine if flux is good or bad. Does it spread evenly across the surface if you drip it onto a metal surface to be cleaned and fluxed? Or does it tend to stick together? Proper spreading indicates good flux.
- Performance: If you notice that your solder isn’t adhering as well as it used to, or if it is forming bridges, it could be a sign that your flux has degraded.
- Storage Conditions: Flux can lose solvents and gain moisture from ambient humidity as it ages, especially if the seal at the cap and plunger is imperfect. As it ages past its expiration date, it may become harder to apply and increasingly tend to spit more when heated.
What happens when flux expires?
As solder flux ages, it can degrade in various ways. This can cause solder paste, which contains flux, to become unworkable. The flux loses its ability to remove oxides on the solder powder, causing the solder particles to stick together. This increases viscosity and can potentially clog stencil apertures and dispensing needles. Flux in small syringes can also lose solvents and gain moisture from ambient humidity as they age. This makes it harder to apply and more likely to spit when heated. The shelf life of unopened brazing flux is typically one year. After this time, the flux may become harder and require the addition of water to restore it to a thick paste consistency.
How does expired flux affect soldering?
Expired flux can hurt soldering quality and performance. Over time, flux can degrade, which may lead to a variety of issues:
- Drying Out: Flux can dry up and harden, making it less effective at cleaning the metal surfaces to be soldered. This can result in poor adhesion of the solder and weak solder joints.
- Loss of Activity: The chemical activators in flux responsible for removing oxides from metal surfaces can lose their effectiveness over time. This can lead to insufficient cleaning of the surfaces, resulting in poor wetting and weak solder joints.
- Change in Consistency: As flux ages, it may change in consistency, becoming either too thick or too runny. This can affect how the flux is applied and how well it works during soldering.
- Increased Impurities: Over time, flux can absorb moisture and other contaminants from the environment, leading to increased impurities in the flux. These impurities can cause defects in the solder joint, such as voids or inclusions.
- Corrosion: Some types of flux, especially those not intended for electronics, can be corrosive and lead to long-term damage to the soldered joints if not properly cleaned after soldering.
In summary, using expired flux can lead to many problems, from poor solder flow and weak joints to potential long-term corrosion. It is best to use flux within its specified shelf life and store it properly to maintain its effectiveness.
How to store soldering flux properly?
To extend the solder flux’s shelf life, storing it properly is essential. Here are some guidelines:
- Temperature Control: Store solder flux at cool temperatures to prevent degradation. Refrigeration is recommended for solder paste, as storage at temperatures above refrigeration can reduce shelf life and void guarantees. Refrigeration may not be required for some types of solder paste, but it should not be exposed to temperatures exceeding 30°C (85°F).
- Orientation: Containers of solder paste, such as syringes and cartridges, should be stored vertically with tips facing down to prevent air introduction. Jars should be stored right side up.
- Sealing: Any opened material should be resealed and stored at room temperature to prevent exposure to heat, moisture, and the atmosphere, which can accelerate paste degradation.
- Avoid Flux Separation: For solder paste, which contains flux, warmer conditions can cause flux separation. If solder paste is left at room temperature for extended periods, the flux and solder may separate, rendering the paste unusable.
- Monitoring: The condition of the paste should be continually monitored to ensure viability for the application. The use of fresh paste daily is highly recommended.
- Transportation and Receipt: Solder paste should be transferred immediately to controlled storage upon receipt. If the packaging includes ice packs, they may arrive melted, which is expected if the 48-hour transport time is not exceeded.
- Expiration and Testing: Respect the expiration date provided by the manufacturer. If you wish to use the paste beyond expiration, re-qualify the material by running test boards or performing appropriate tests.
In conclusion
Our guide on soldering flux reveals that although it does not spoil like food, it degrades over time. This degradation can affect the quality of your soldering work, resulting in weaker joints and potential long-term damage to the soldered components. To avoid these risks, storing the flux properly and being mindful of its condition and expiration date is vital. Managing the shelf life of soldering flux is not just about a simple time frame but also about proper care throughout its lifecycle. To maintain high soldering standards of your soldering machine, ensure the fresh flux is stored adequately.